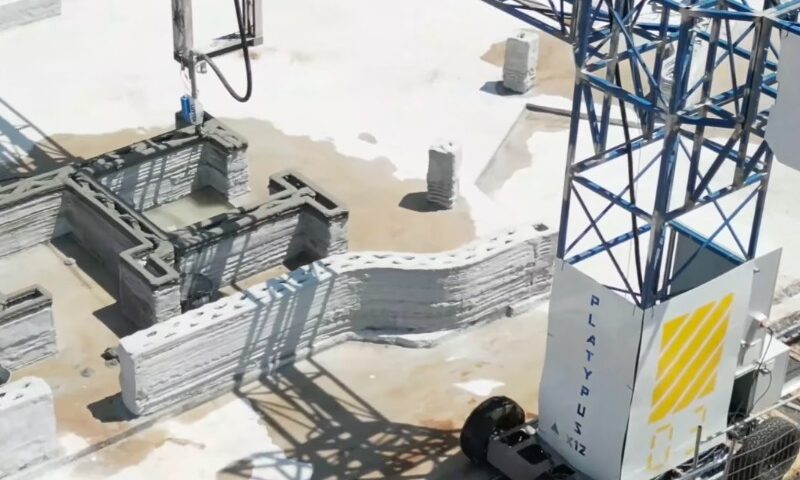
The Revolution Begins: 3D Printing Meets Homebuilding
On a quiet street in Wyndham, a suburb on Melbourne’s western outskirts, an unusual home is taking shape. Unlike traditional brick-and-mortar houses, this one isn’t being built with hammers, nails, or wooden frames. Instead, a giant robotic crane methodically extrudes layers of concrete, forming walls that resemble soft-serve ice cream.
This isn’t just any home—it's Australia’s first 3D-printed multistorey house. And it’s being built in record time.
Why 3D Printing? Addressing Australia’s Housing Crisis
Housing shortages and skyrocketing prices have plagued Australia for years. Construction timelines have only worsened, with standalone houses now taking an average of 12.7 months to complete—40% longer than they did 15 years ago. Apartment construction fares even worse, often stretching beyond 33 months.
Ahmed Mahil, CEO of Luyten, the company behind this groundbreaking project, believes 3D printing could be the solution. And he’s putting his money where his mouth is—this home will be his own residence.
«I'm not just selling it to people, I actually trust the science behind it.»
The numbers are compelling. Mahil’s four-bedroom, five-bathroom home will be completed in just five weeks, with the actual printing taking only three.
Faster, Cheaper, and More Efficient? The Cost Factor
Traditional construction methods aren’t just slow—they're expensive. While there’s limited Australian data comparing costs, Mahil says he gathered multiple quotes for the same house. The results?
3D printing came out 25−30% cheaper than conventional building methods.
Though he didn’t disclose the exact figures, this kind of cost reduction could make homeownership more accessible in the long run.
Global Trends: 3D Printing Beyond Australia
Australia isn’t the first to explore 3D-printed housing. In 2023, a single-bedroom house in New South Wales was printed in just two days. Overseas, entire communities are being built this way. In Texas, a 100-home neighborhood was printed last year, demonstrating the potential scale of this technology.
Governments are taking notice. In Dubbo, New South Wales, a 3D-printed public housing project is nearly complete. Two duplexes, designed for Indigenous tenants, were built in just two weeks. The project is expected to cost 10−20% less than traditional builds.
«It's faster to construct, cheaper to build, and reduces material waste,» says NSW Housing Minister Rose Jackson.
Environmental and Logistical Challenges
Beyond cost and speed, 3D printing has the potential to be more environmentally friendly. A recent study in Canada highlighted its sustainability benefits, particularly in remote locations. However, it also pointed out areas for improvement, such as material transport and energy efficiency.
There are other challenges too. Property developer Kavitha Vipulananda, currently completing a PhD in housing, notes that while 3D printing works well in suburban areas, inner-city construction remains tricky due to printer size and maneuverability.
«Right now, it’s mostly limited to houses, not large-scale urban developments.»
Additionally, banks remain cautious about financing 3D-printed homes due to the technology’s novelty. Consumers also have fewer design customization options compared to traditional builds.
Will 3D Printing Reshape the Future of Construction?
Michael Fotheringham, managing director of the Australian Housing and Urban Research Institute, sees potential but remains cautious.
We’re still in the early days. Right now, we’re demonstrating possibilities rather than mainstream implementation.
For 3D-printed homes to become the norm, more research is needed on insulation, energy efficiency, and long-term durability. Governments also need to focus on high-density housing near city centers, where demand is highest.
Still, one thing is clear—3D printing is no longer just a futuristic idea. It’s here, and it’s building homes today. The question is, how far will it go?