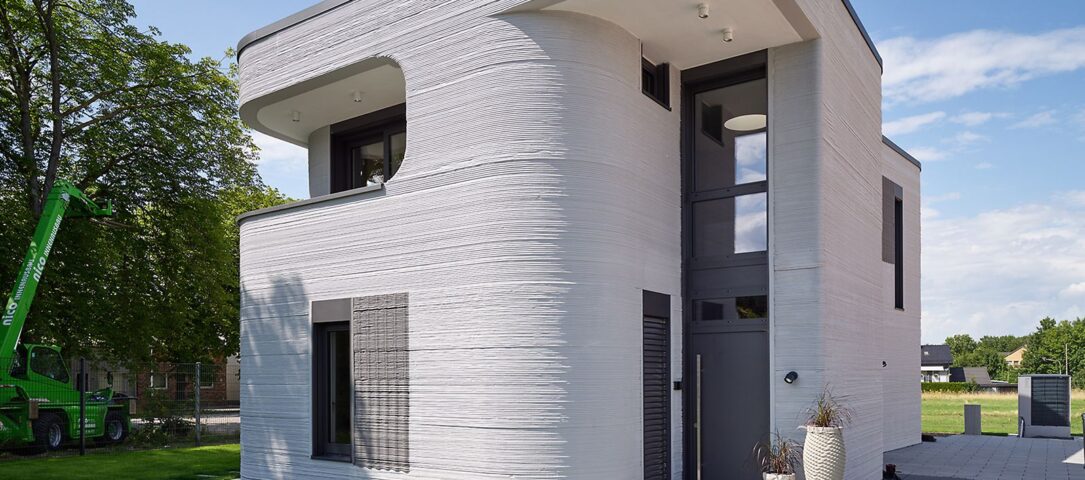
3D printing is no longer just for prototypes and small objects—it's now building entire homes. With its ability to cut costs, reduce waste, and speed up construction, this technology is revolutionizing the housing industry. While traditional methods rely on heavy labor, extensive materials, and long timelines, 3D-printed homes can be built in days instead of months. Let’s explore five key technologies driving this transformation.
Concrete Extrusion: The Backbone of 3D Construction
Concrete extrusion is the most widely used method in 3D-printed construction, forming the foundation of many large-scale, durable, and cost-effective building projects. This technique involves layer-by-layer deposition of a specially formulated concrete mix, creating structurally sound walls and entire buildings with minimal waste and labor.
How It Works
Unlike traditional poured concrete, which requires molds and formwork, concrete extrusion relies on a computer-controlled nozzle that precisely deposits material based on a digital blueprint. This allows for greater design freedom, enabling curved walls, organic shapes, and intricate patterns without additional materials.
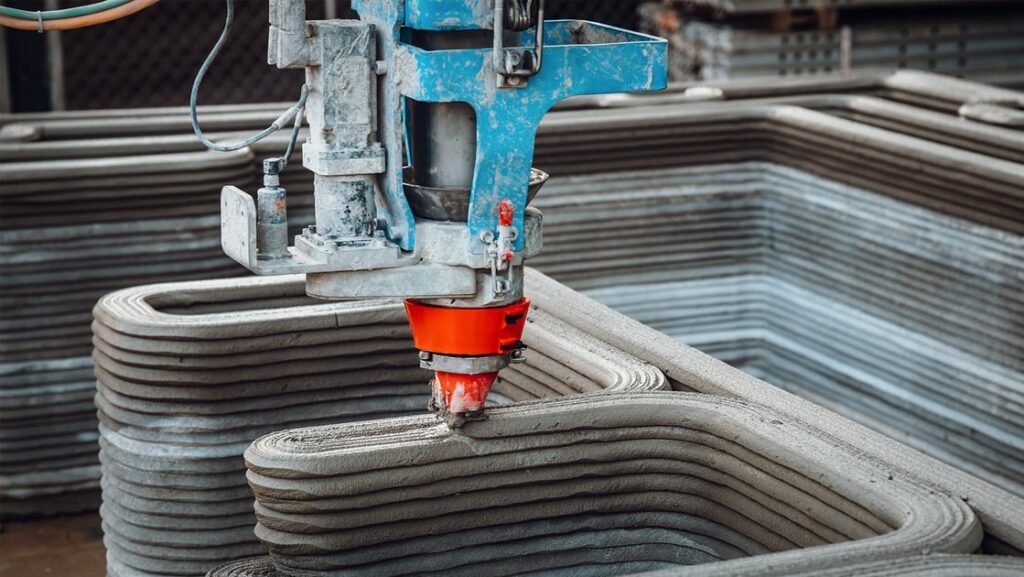
The concrete mix used in extrusion is optimized for rapid setting, ensuring that each layer bonds securely without collapsing. These mixtures often include fiber reinforcements or additives to enhance strength, flexibility, and weather resistance.
Compared to conventional construction, 3D-printed concrete structures can be built **30−50% faster** while reducing material waste by up to **60%**.
Real-World Applications
One of the most famous examples of concrete extrusion is COBOD’s BOD2 printer, which was used to construct Europe’s first multi-story 3D-printed building in Germany. The printer’s ability to extrude concrete precisely and continuously allowed for rapid construction, significantly cutting down labor costs.
Another remarkable case is ICON’s 3D-printed homes in Texas, where concrete extrusion was used to build affordable, hurricane-resistant houses. The project demonstrated how this technology could address housing shortages while maintaining structural integrity and energy efficiency.
Concrete extrusion is especially beneficial for **disaster relief and affordable housing**, as it enables **fast, scalable construction with minimal human labor**.
Advantages and Challenges
The biggest advantage of concrete extrusion is its ability to automate and accelerate construction, making it an ideal solution for mass housing, commercial buildings, and infrastructure. It also reduces the need for traditional formwork, lowering material waste and overall costs.
However, this technique still faces challenges. The limited mobility of large-scale printers means that on-site assembly can be complex, requiring precise setup and calibration. Additionally, while concrete extrusion is strong, it often needs reinforcement with steel, rebar, or hybrid materials to meet building code requirements for multi-story structures.
Despite these obstacles, concrete extrusion remains the cornerstone of 3D-printed construction, continually evolving to improve strength, reduce costs, and expand design possibilities. With ongoing advancements in robotics, AI, and sustainable materials, this technology is set to redefine the future of architecture and infrastructure worldwide.
Sand and Geopolymer Printing: A Sustainable Choice
Traditional concrete-based 3D printing has made significant strides in construction, but it still heavily depends on cement, a material responsible for nearly 8% of global CO₂ emissions. In contrast, sand and geopolymer printing offers a more sustainable and eco-friendly alternative, utilizing natural aggregates and industrial by-products to create durable, low-carbon structures.
How It Works
Instead of cement, geopolymer printing relies on geopolymer binders—materials derived from fly ash, slag, or other industrial waste—which significantly reduce carbon emissions while maintaining high strength and durability. When combined with locally available sand or other fine aggregates, these binders form a strong, heat-resistant, and eco-friendly building material.
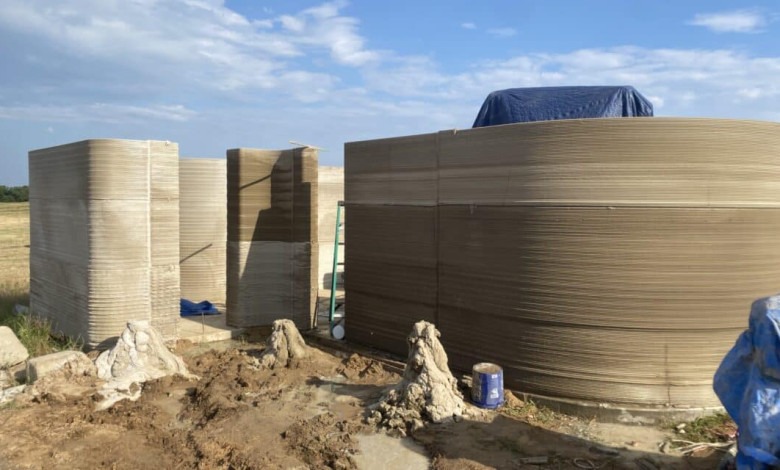
One of the major advantages of this method is that it eliminates the need for high-temperature kilns, further cutting energy consumption. Additionally, geopolymer-based structures can withstand harsh environmental conditions, making them ideal for coastal areas, deserts, and regions prone to extreme weather.
By replacing cement with geopolymer binders, construction-related **CO₂ emissions can be reduced by up to 80%**, making this one of the most sustainable 3D printing techniques.
Real-World Applications
A leading example of geopolymer 3D printing in action is Tecla, an eco-friendly 3D-printed home in Italy. Developed by Mario Cucinella Architects and WASP, this project used locally sourced clay and geopolymer materials to build a biodegradable, low-carbon dwelling, proving that sustainable 3D printing is not just a concept but a reality.
Another promising case is research from RMIT University in Australia, where scientists have successfully 3D-printed structures using a geopolymer mixture derived from mining waste. Their findings show that this material offers comparable or even superior strength to traditional concrete while being far more environmentally friendly.
Sand and geopolymer printing isn’t just sustainable—it also provides **better thermal insulation**, helping to reduce energy consumption in buildings.
Advantages and Challenges
The primary advantage of sand and geopolymer printing is its eco-friendliness, as it utilizes waste materials and reduces reliance on energy-intensive cement production. Additionally, geopolymer-based materials are known for their high durability, fire resistance, and improved thermal properties, making them well-suited for sustainable housing and infrastructure.
However, the technology is still evolving, and material costs can be higher due to limited availability and production of geopolymer binders. Additionally, regulatory approval and standardization are needed to encourage widespread adoption.
Despite these challenges, sand and geopolymer 3D printing is paving the way for a greener future in construction. As research continues, cost reductions and wider availability of geopolymer materials could make this one of the most viable solutions for sustainable, large-scale 3D-printed housing and infrastructure.
Foam 3D Printing: Lightweight and Energy-Efficient
Foam 3D printing is a cutting-edge construction method that focuses on lightweight, highly insulated structures. Unlike traditional concrete-based printing, this technique uses foamed cement, polymer foams, or aerated materials to create energy-efficient and soundproof buildings. The result is a construction process that is not only faster and more cost-effective but also significantly reduces material usage and environmental impact.
How It Works
Foam-based printing materials are formulated to be lightweight yet durable, often incorporating air pockets or microbubbles to enhance thermal and acoustic insulation. These materials are extruded through specialized nozzles, layer by layer, to form walls and structural elements.
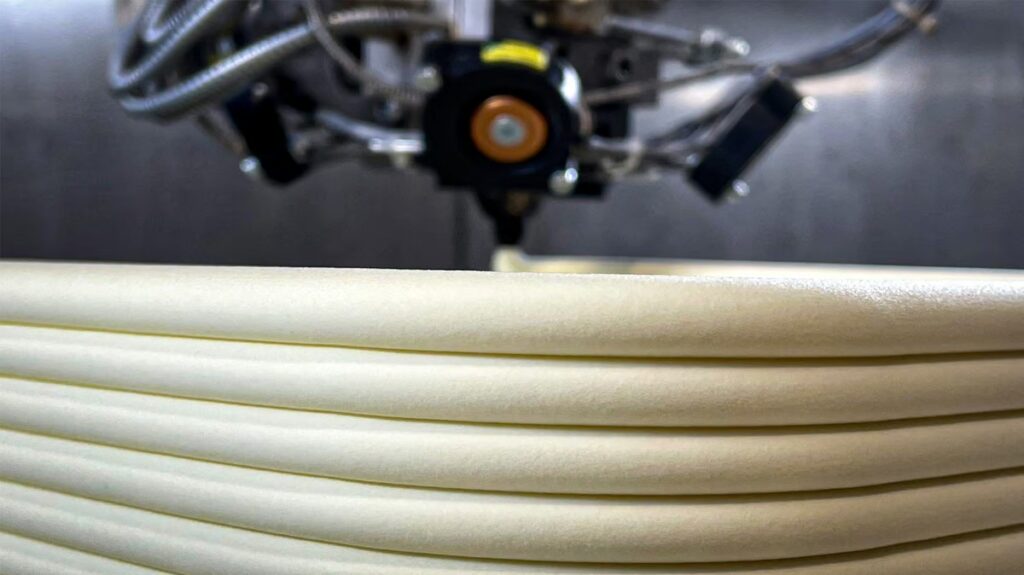
A key advantage of foam 3D printing is that it allows for quick, large-scale construction while minimizing structural weight. This makes it an ideal choice for temporary shelters, prefabricated housing, and disaster relief structures. Additionally, because foam materials provide excellent insulation, buildings require less energy for heating and cooling, making them more sustainable in the long run.
Foam 3D-printed buildings can achieve **up to 60% better insulation** than traditional concrete structures, drastically reducing energy costs.
Real-World Applications
One of the most impressive uses of foam 3D printing is the construction of modular, self-sustaining homes. Projects like Haus.me have demonstrated how foam-based materials can be used to create off-grid, highly energy-efficient living spaces. These homes combine advanced insulation with solar power, enabling them to operate independently in remote locations.
Another pioneering example is the University of Nantes' Yhnova House, a fully 3D-printed home using an insulating foam and concrete hybrid technique. This project highlighted how foam printing can be combined with traditional materials to enhance durability while maintaining energy efficiency.
Foam-based 3D printing isn’t just about insulation—it also enables **lighter, more flexible structures**, making it useful for **earthquake-resistant buildings**.
Advantages and Challenges
The biggest benefit of foam 3D printing is its lightweight nature, which allows for faster assembly and reduced transportation costs. It is also an excellent choice for sustainable construction, as fewer raw materials are needed compared to conventional methods.
However, foam printing also presents structural limitations. Since foam materials lack the strength of traditional concrete, they often require additional reinforcement using steel beams, wooden supports, or hybrid materials. Another challenge is weather resistance, as some foam-based materials may degrade over time if not properly treated.
Despite these hurdles, foam 3D printing is gaining traction as a sustainable and efficient building technique. As material science advances, stronger and more weather-resistant foam formulations are being developed, making this method a promising solution for affordable, energy-efficient, and rapidly deployable housing.
Robotic Arm and Gantry Systems: Precision and Flexibility
Unlike traditional large-scale 3D printers that rely on a fixed frame and rails, robotic arm and gantry systems offer a more flexible and precise approach to 3D printing in construction. These systems use either multi-axis robotic arms or movable gantries to print complex structures with higher precision than standard extrusion methods. This makes them ideal for projects requiring customized architectural designs, intricate details, or multi-material construction.
How It Works
Robotic arm systems are highly maneuverable and can rotate and move in multiple directions, allowing them to print structures that are not limited by a rigid track or fixed printing area. This flexibility enables the creation of curved walls, overhangs, and organic shapes that traditional 3D printers struggle with. Additionally, robotic arms can switch between different nozzles, allowing for multi-material printing, such as combining concrete with insulation layers or reinforcement fibers.
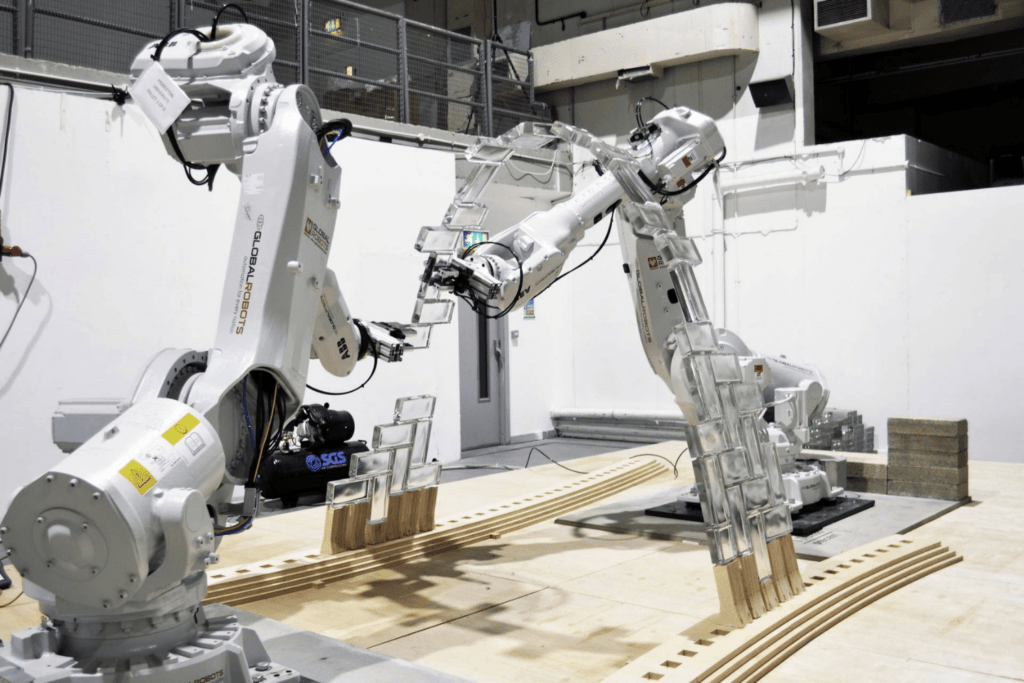
Gantry systems, on the other hand, operate on a large, rail-based framework, making them suitable for printing larger structures like entire houses or multi-unit buildings. These systems provide a balance between precision and scalability, ensuring uniform layer deposition while maintaining structural integrity.
One key advantage of robotic arm 3D printing is its ability to construct **freeform designs** that push the boundaries of traditional architecture.
Real-World Applications
A groundbreaking example of robotic arm 3D printing is ETH Zurich’s DFAB House, where a multi-axis robotic arm was used to create intricate concrete structures with ultra-thin, optimized designs. The project demonstrated how robotic printing can reduce material usage while maintaining strength, resulting in more sustainable construction.
Gantry-based systems have also made headlines, such as COBOD’s BOD2 printer, which was used to build Europe’s first 3D-printed multi-story building in Germany. This system allowed for the precise layering of concrete, ensuring a strong and durable structure while significantly reducing construction time.
By integrating AI and automation, robotic arm and gantry systems can **adapt to real-time construction challenges**, improving efficiency and accuracy.
Challenges and Future Potential
While robotic arm and gantry systems offer unmatched precision and design flexibility, they come with challenges. Robotic arm setups require advanced programming and specialized workforce training, increasing initial costs. Gantry systems, while scalable, still rely on fixed rail structures, limiting mobility.
However, as automation, AI, and material science continue to evolve, these technologies are expected to become more accessible and cost-effective. In the near future, fully autonomous robotic 3D printing systems could be deployed for on-site, large-scale construction projects, further reducing waste, labor costs, and environmental impact.
Hybrid 3D Printing: The Best of Both Worlds
While 3D printing alone offers significant advantages in speed and efficiency, it still has limitations when it comes to structural strength, insulation, and long-term durability. That’s where hybrid 3D printing comes in—a method that combines additive manufacturing with traditional construction techniques to create stronger, more versatile, and cost-effective buildings.
How Hybrid 3D Printing Works
In hybrid construction, 3D-printed components—such as walls or structural frames—are combined with conventional materials like steel reinforcements, insulation panels, or prefabricated roofing systems. This approach enhances durability while maintaining the speed and efficiency of 3D printing.
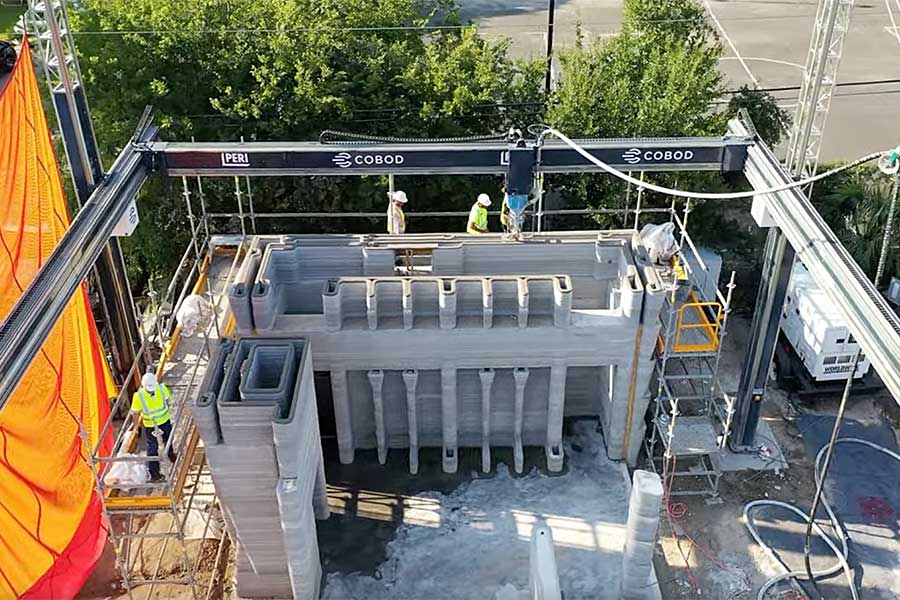
A common technique is to print the main structure using concrete extrusion, while integrating steel beams, wooden supports, or modular panels for added strength and thermal performance. This makes hybrid construction more adaptable to different climates and building regulations, as it retains the benefits of both digital fabrication and traditional craftsmanship.
Hybrid 3D printing allows for **faster construction without compromising on quality**, making it a practical solution for large-scale housing projects.
Real-World Applications
One of the best examples of hybrid 3D printing is PERI’s 3D-printed apartment building in Germany, which was constructed using a combination of printed concrete walls and traditional reinforcement techniques. This allowed for a multi-story structure with increased stability, something that pure 3D printing methods still struggle to achieve.
Another notable case is SQ4D's 3D-printed house in New York, where printed walls were reinforced with conventional wood framing to meet local building codes. The hybrid approach ensured that the home was not only fast and cost-efficient to build, but also met safety and insulation standards.
By integrating **traditional reinforcements**, hybrid 3D-printed homes can comply with **building codes and zoning laws**, making them more viable for mass adoption.
Advantages and Challenges
The biggest advantage of hybrid 3D printing is that it enables the scalability of 3D-printed homes while maintaining structural integrity. It also reduces material waste, as only essential structural components are traditionally built, while the rest is 3D-printed.
However, the method still relies on human labor for assembling non-printed components, which adds some time and costs compared to fully automated printing. Additionally, coordinating between 3D printing and traditional construction crews requires careful planning to avoid delays.
Despite these challenges, hybrid 3D printing is emerging as a realistic and scalable solution for mass housing production. By combining the speed of automation with the reliability of traditional materials, this technology could reshape the future of construction, making homes faster, cheaper, and more adaptable to different environments.
3D printing is already reshaping the construction industry, making homes faster to build, more affordable, and more sustainable. While challenges like regulation, material limitations, and skilled workforce requirements remain, ongoing advancements are bringing us closer to a future where 3D-printed homes become mainstream. The real question is—how long before this technology builds your next home?